Designing Plastic Parts
Guidelines for Plastic Injection Molding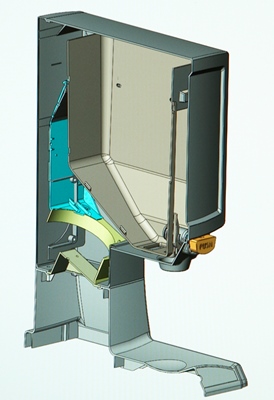
Retlaw Industries has been manufacturing plastic parts for nearly 40 years now, and our clients trust our knowledge of the craft. Consideration needs to be put into each step of the injection molding process, and we strive to help you better understand how your plastic part is precision manufactured to create the result you need.
Plastic molded parts can vary in size, shape, and complexity, but Retlaw’s CNC engineers know exactly how to produce high-quality custom plastic parts that meet client needs. To best manufacture a custom part, it takes following laid out design steps. That's why we strive to help our clients better understand injection molding concepts so the product they receive best matches the intended use case.
Here are some important guidelines to consider when we manufacture your thermoplastic part:
Injection Molding Materials
Determining which thermoplastic resin is used for your molded part depends on what the part is used for. For example, certain plastics may have good tensile strength for strong impact resistance, while others are better at withstanding extreme temperatures like hot and cold.
- Surface Finish – Industry-standard finishes are available for most plastic injection molded parts, including texturing and polishing. Whichever surface finish you have will depend on the material used on your plastic part.
The experts at Retlaw will help you make the best decisions regarding your custom plastic component’s material makeup.
Wall Thickness
When manufacturing plastic molded parts, the amount of plastic used in the mold’s walls helps them avoid potential issues such as sink marks and warpage, which can be damaging to the overall structure of the plastic. The wall thickness of a molded part can vary depending on the plastic resin used to create it and the size of the part in question.
- Ribs – In-molded thermoplastic designs, ribs are often manufactured to reinforce the walls of a plastic part. Ribs are useful when wanting to increase the strength of a part without adding to the overall wall thickness, and ribs often need to be taken into consideration when designing a particular plastic part.
Walls designed to be too thick wastes material, money, and can negatively affect part performance. Retlaw’s designers will help your product strike the balance between proper function and cost-efficiency.
Draft
The angle at which plastic parts are removed from their mold is known as the draft, and it is vital to the overall structure of the plastic part. A “vertical” draft can be detrimental to the plastic part in question, therefore CNC engineers understand a degree of the draft is necessary when manufacturing and removing a plastic part from its mold.
Radius
The radius of a plastic part refers to the sharpness of the edges of each corner. Edges that are too sharp can greatly increase stress concentration, which could actually lead to eventual part failure. Sharp corners need to be rounded slightly in order to lessen the stress concentrations, meaning the edge’s radius needs to be taken into consideration when manufacturing a molded part.