ABS Plastic Injection Molding
Retlaw Industries manufactures high-quality ABS thermoplastic components for a wide range of applications. ABS is a versatile plastic product due to its affordability and resistance to strong impacts and corrosive chemicals. It is also relatively harmless with no known toxic carcinogens.
What is ABS Molding Material?
ABS (Acrylonitrile Butadiene Styrene) is a thermoplastic polymer. ABS is made from three monomers: acrylonitrile, butadiene, and styrene. It is often used in the injection molding process and is one of the most common plastics used in OEM part production and 3D print manufacturing.
Why is ABS So Commonly Used?
ABS is commonly used due to its combination of its low-melting point, high-tensile strength, and robust resilience. ABS is commonly used in plastic injection molding and allows for a finished product with the resilience to withstand real-world use in adverse environments.
ABS Material Characteristics
The chemical properties of ABS plastic give it a relatively low melting point and a low glass transition temperature, meaning it can be easily melted down and molded into different shapes during the injection molding process. ABS can be repeatedly melted down and reshaped without significant chemical degradation, making the plastic recyclable. Other benefits of products made of ABS plastic include:
- Strong impact resistance
- Strong heat resistance
- High tensile strength
- Shock absorbance
- Scratch resistance
- Low cost
ABS is relatively safe to handle as it cools down and hardens. This makes it one of the easiest plastics to handle, machine, paint, sand, glue, or otherwise manipulate.
Contact Retlaw Industries for a quote on manufacturing plastic injection molded ABS parts.
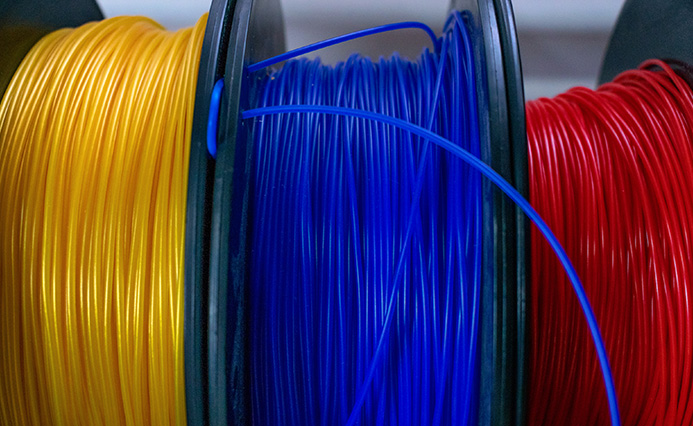